Q&A: Castrol’s Rachel Howard
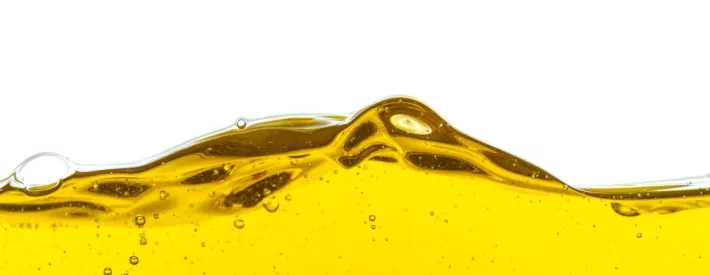
Combustion engines will remain part of the industry for many years to come, so they need to run smoothly and efficiently. Castrol’s Senior Manager for Technology Deployment for Lubricants explains the exhaustive process that goes into designing, developing and testing a new engine oil.
How are key requirements and performance goals for a new premium lubricant product defined?
There can be a very wide range of inputs, though most typically, the impetus for the creation of a new formulation comes from one of two sources – either from a formal collaboration with an OEM for the co-engineering of a ‘first fill’ product (i.e. a lubricant that will be introduced into the engine at point of manufacture), or we are responding to one of the new lubricant specifications that many OEMs will publish.
With a new first-fill formulation, we will be liaising with the OEM’s powertrain engineers from a very early point in the vehicle’s development. OEMs work with Castrol to define the recipes of base oils and additives that will protect engine components against energy-sapping wear and friction, while also enabling oil change intervals to increase. The new lubricant forms an integral component, helping to meet current and predicted regulatory requirements and specifications.
The more common route is for us to develop a new lubricant to meet a new specification that the OEM has published. This might be a response to new legislation or stipulations from regulatory bodies, such as changing emissions requirements, or it might result from an OEM’s efforts to further optimise fuel efficiency, boost power or drive down emissions. In these instances, the OEM publishes its specification, and our account managers liaise with the OEM to best understand the specific requirements before we commence any work.
How long does it typically take to develop a new oil – from initial plan to having a first-fill or service-fill product ready to commercialise?
It’s a real balancing act to find the right types and quantities of components that deliver the low viscosity required for fuel economy and emissions, and yet at the same time provide the kind of robust protection against wear and resist the build-up of sludge and deposits. What works well for one performance criteria can sometimes have a negative impact on another
To meet a number of challenging new industry requirements, we have recently been working on three important long-life variants: 0W-20, 0W-30, and 5W-30, which together cover 16 different OEM and industry specifications. That programme has been complex and necessarily quite protracted, requiring more than 110 engine tests with over 35,000 engine running hours, coupled with over 100 laboratory test cycles.
It has been possible to achieve our core objectives for these products specifically because we have been able to deploy the resources and talents of the wider Castrol operation in three countries. That programme has represented a multi-million-dollar investment for each of those three new products.
Isn’t it easier to just create separate OEM-specific formulations?
The lubricant is one of the few things that is seen as a critical area where advances in engine performance can continue to be realised, such as via extended oil drain intervals, greater fuel economy, durability and cleanliness. The targets keep being changed, new specifications are published, and new lubricants have a more difficult job than ever to do.
How have development and test processes been influenced by the shift towards lower viscosities?
Vehicle manufacturers are creating smaller yet more powerful engines. Turbocharging maintains power but increases the amount of pressure inside the engine. As a result, lubricant performance is being challenged more than ever before.
Fuel economy and improved power is dependent on formulation design where low viscosity is one of the primary contributors, and that has given rise to an unrelenting drive for ever-thinner lubricants. Our own development efforts are often focused on meeting new performance targets with lower viscosities. We’re also learning from our collaborations with motorsport teams, where the development of bespoke engine oils of the lowest viscosities has become critical for meeting their performance and durability goals.
We always test for the most demanding applications with low viscosities. We then know that any specification not requiring such a thin lubricant can then be met with many of the same core components. Delivering Edge products at 0W-16 and 0W-20 is inherently very demanding, and it is often the starting point for us in meeting a new specification.
What proportion of the product development can be achieved through simulation versus real-world testing?
While we’ve made huge progress in the overall performance of Castrol’s Edge lubricants, the test process itself has not seen a radical shift towards simulation. It remains the case that 100% of the validation process has to be engine-based; you need that physical reference point to gain absolute certainty about outcomes. Simulation can only tell you so much about the interplay of incredibly complex ingredients, and OEMs always demand real-world physical testing before sign-off.
However, it is important not to underestimate the importance of computerisation in lubricant development, particularly over the past few decades. This isn’t to facilitate simulation; rather it is to facilitate the management of extraordinary volumes of data points from previous test processes. This data helps us identify trends and benefits that informs every new programme. This statistical analysis of historical data can also be used to model performance for new experimental oils – for some specific performance parameters. This can sometimes be more accurate than the original engine or laboratory test. We are increasingly using modelling to determine performance for our newly developed oils.