The battery remains the beating heart of any vehicle
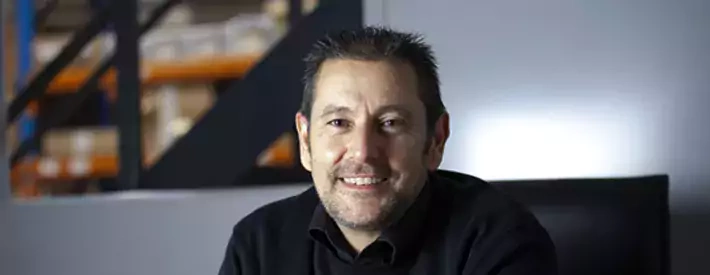
Advertorial: There are training courses aplenty covering all aspects of electrification, vehicle maintenance and repair for established and aspiring vehicle workshop technicians. To be EV-ready is no mean feat as there is still so much unknown about this technology; but what a great journey it is to be on.
Rotronics is right at the centre of all things relating to batteries and the move to EV is very much at the forefront of the Team’s thinking, because EV technology relies on the same 12v and 24v battery systems as any combustion vehicle.
Ken Clark, Managing Director at Rotronics, comments: “In electric vehicles, we are still seeing battery failure and battery neglect. Unfortunately, there is a perception that, because the batteries are not required for cranking, no maintenance is required. This couldn’t be further from the truth; the same battery care and maintenance is required as it has always been.
“There is one major difference however that we must consider. Traditional ICE vehicles needed battery power primarily for starting (or cranking power), with the exception of Hybrid and Start/Stop vehicles, whereby reserve capacity also plays a significant role in the ability of the battery to support the electrical systems.
“BEV 12V batteries have no use for cranking power and are merely there to provide power (AH) to support the vehicle’s electrical system. We therefore have to change the way in which we test these batteries, to include the ability to not only measure cranking ability, but also reserve capacity.”
Workshops now need to ensure their battery testing equipment is up to date to support these changing technology requirements.
Check out the latest testing technology platforms, the CPX900 and the DCA8000 that use a combination of cranking and reserve capacity testing, known as conductance profiling, that meet the needs of both today’s and tomorrow’s vehicles.
It therefore remains to be said that keeping batteries tested and charged up is more important now than ever.
Ken Clark continues: “With vehicles no longer needing large batteries to support the cranking of engines, we are seeing significantly smaller batteries being used. As an example, a 24V set of batteries in a traditional ICE PSV would have been circa 180-220Ahr, and this has now been replaced with 2 x 65Ahr batteries.
“Because of the reduced reservoir of power, the same combustion engine battery maintenance is proving to be essential to support the system. The battery remains the beating heart of any vehicle and the drain on batteries is likely to be more in an electric vehicle, so this is no time to take our eyes off testing and charging.”
Powerpacks are still relevant for use with electric vehicles, in instances when the 12V battery goes flat. The powerpack is then used to enable the electronics that manage the charging process to operate first and then charge the 12V battery itself.
Ken Clark says: “Contrary to what you may believe, the roadside breakdown organisations continue to attend numerous BEV breakdowns where the 12V battery is at fault. Largely, as a result of being discharged. This is a clear reason why the 12V battery remains at the heart of the electrical system of all ICE and BEV vehicles.”
Top Testing and Charging Tips
- Test and charge every vehicle coming into your workshop for routine maintenance
- Have test and charge technology in every bay if you are in a CV workshop
- The Rotronics customers who follow this rule have the best performing batteries, therefore the lowest number of roadside defects
- Charge all stock batteries on the shelf, every month
- Make sure that the batteries are balanced (for commercial vehicles)
- Imbalanced batteries are a bit like an irregular heartbeat
- They have a reduced lifespan of up to 50%
- Without regular maintenance, a battery set can be out of kilter
Find out more about Rotronics testers, chargers, and powerpacks.
Over 70% of Batteries Need Charge or Replacement
Battery imbalance and poor maintenance can contribute up to 50% of a workshop’s annual battery-related costs. From the 286,000 battery tests recorded so far in 2022, only 28% are in a good and healthy condition. This means that over 70% are either in need of charge or replacement, to prevent a roadside defect. 65% of all commercial vehicles tested have batteries that are out of balance and will fail prematurely if this is not rectified.
The 12V and 24V battery sets in a passenger car or a commercial vehicle in a BEV application remains one of the most important components that if not maintained will cause the vehicle to break down.
To seek further advice from the Rotronics team, regarding products available and the battery management programmes, email info@rotronicsbms.com or go to www.rotronicsbms.com or alternatively, call Ken Clark on 0121 514 0605.