Apprenticeships: The funding challenge
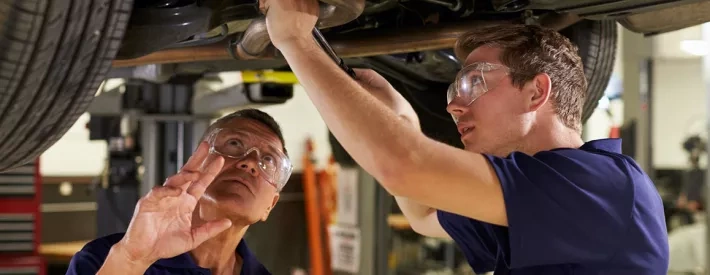
In this article: Apprenticeships are a crucial part of the industry, but there are challenges to be fixed, most notably paying for them. But why is funding such an issue?
Vocational training has been a staple of Britain’s automotive industry since Frederick Simms started making petrol-powered cars in 1895. However, in recent years, take-up has actually dipped. The number of people starting apprenticeships in England fell by 7% in the first half of 2019/20.
The most contentious part of the problem is the Apprenticeship Levy, which funds apprenticeships in England. Introduced in 2017, it requires employers with wage bills of more than £3m to set aside the equivalent of 0.5% for vocational training.
The levy
The issue is that the cash is not being spent in the right places. Businesses argue that the complexity and strictness of the levy system stops them from using it to train the types of apprentices they need. The 2017 reforms included, for instance, a switch from old-style apprenticeship “frameworks” to “standards”. While the new standards are created by employer groups and include an End-Point Assessment, they do not suit every business’s needs, and the approval process for any changes is too slow for this fast-moving industry. “To date, the logistics sector has paid more than £410m into the levy pot, but just 10% of that has been drawn down, mainly because there are no appropriate standards,” the FTA’s de Jong says.
To make matters worse, if levy money is not spent within 24 months, it is taken by the Treasury as a stealth tax. The IMI fears that the levy is now inadvertently creating a funding crunch just as the stricken motor industry emerges from lockdown, at a time when it desperately needs to upskill its workforce to meet the government’s tough emissions targets.
Simon Ashworth, Chief Policy Officer at the Association of Employment and Learning Providers, says that companies are now racing to spend their levy contributions to avoid gifting them to the government. But this trend is driving a shift towards training for older, existing employees taking more expensive qualifications at the higher levels, ignoring the young people that the industry really needs.
Indeed, a report last year from the think tank the Resolution Foundation warned that the levy was “crowding out” youngsters, with the number of lower-level apprenticeships reducing by 45% between 2014/15 and 2017/18.
And even though lower-level apprenticeships aren’t taking their share of the levy money, the rise of pricey degree-level apprenticeships (including MBAs) threatens to blow a hole in the apprenticeship budget, which could be overspent by as much as £1.5bn by 2021.
Meanwhile, the private companies that provide training for 70% of apprenticeships in England are also coming under acute financial strain because of the lack of new apprentices and a dearth of government funding. This is limiting their capacity to deliver training and leaving companies with fewer options. Many smaller, non-levy-paying companies, which make up the bulk of the motor industry, were already struggling to find training because the providers are increasingly focusing on the bigger levy payers. It’s a trend that’s sadly driven by straightforward financial necessity.
The government pays for most of the training costs of smaller firms through the levy pot, but the big levy payers have first dibs on this already overstretched funding. “There’s almost a disincentive for training providers to work with the small employers that get the leftover crumbs,” Ashworth explains.
The result of all this is that there were 171,400 fewer apprenticeship starts in 2018/19 than before the levy rolled out. The government has also failed to reach its 2015 target of creating 3 million new apprenticeships by 2020.