The EV revolution: it’s all in the training for the body repair sector
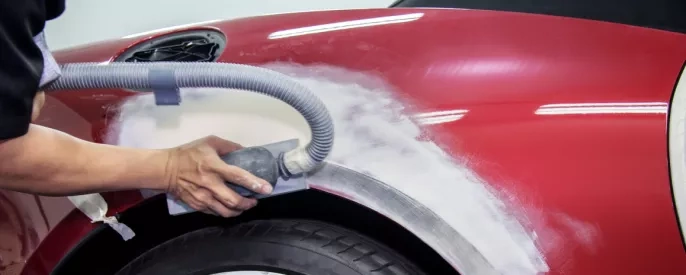
The repair sector has been changing for some time with manufacturers winding down combustion engine production and instead focusing on the research, development and production of electric. This poses many new challenges for not only repairers on the ground, but emergency services, vehicle recovery, and mechanics – none more so than the safety aspects involved in managing and safely discharging the electrical charge ahead of conducting any works.
Director at Mackins Accident Repair Centre Ltd UK, Patrick Mackin, says: “The first step for any repairer should be the safety of their staff working on these vehicles. That’s where training and appropriate equipment and tooling comes in. Manufacturers have so many features to add to the driving experience and without the awareness of these bodyshops run the risk of unintentionally damaging some of the systems which ultimately has the potential to end up costly if the need for an electronic repair is required.
“In our own bodyshop we had recognised and predicted the rise in EV vehicles coming through some time ago. The distinct advantage we had was our nine manufacturer approvals - we were continually kept in the loop of developments and our staff were constantly training and learning the correct procedures required to carry out a safe repair ensuring all systems were properly reinstated after completion.
“Our staff are currently Level 3 ATA trained in repairing electric vehicles and we plan to train an additional two staff members in Level 4 to future proof our business. This allows us to keep everything in-house meaning we have full control over the flow of each repair – we are not waiting on dealers having to investigate or reinstate systems – with our staff’s knowledge bank, we are able to sort most on site. For those few jobs that we can’t, we have the option of dealer dial in through Repairify who have full access to most manufacturer diagnostic equipment so regardless of what situation or challenge we face we have the coverage and knowledge for a successful resolution.”
Director and bodyshop manager at Summers Motors, Ian Summers, agrees that the way forward is manufacturer-approval: “With the increased sales of EVs it was inevitable that bodyshops would see a sharp increase going through their shops. There are varied training courses covering safety, basic knowledge and awareness but correct VM repair methods, tooling and equipment are 100% necessary for safeguarding the tech, the vehicle and ultimately the business. As a VW Group-accredited bodyshop, our senior MET had to undertake 22 separate online modules, along with two virtual classrooms, and four days of face-to-face training for a qualification on only VWG vehicles and that was supported by us investing in around £15k worth of equipment and tooling,” he says.
“As EVs develop, with more complex vehicles gracing our roads, it will become more likely that repairers will have to be aligned with a VM to be able to carry out full shut downs and those that aren’t even with having invested in a serious amount of training and equipment will still be limited to how much they can do. There still seems to be a massive lack of understanding around EVs but what is in no doubt is the risks to the battery if work is carried out by an untrained tech without access to correct repair methods and equipment.”
Mackin is sure that businesses need to be prepared for whatever the future holds: “From a personal point of view, I can’t stress enough the importance of foresight, now more than ever – it’s better to be proactive when you can plan for situations and come up with sustainable resolutions than reactive when you are already on the back foot. That’s why we’ve put ourselves in such a great position to manage any EV jobs that come in in-house,” he says.
Want to get EV-ready, look at the route to the IMI’s TechSafe recognition