Gain access to the right fault-finding data
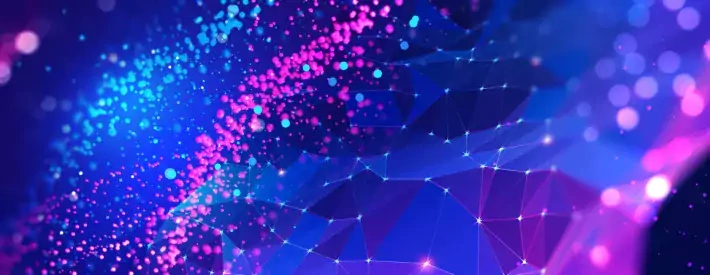
With manufacturers constantly changing and updating the way their systems work, diagnosing vehicle faults has never been so difficult. Hard-to-get or unreliable information we rely on to diagnose vehicles can cause aftermarket workshops a real headache.
From my research, all the data is out there somewhere. It just costs money to get that data and requires a deep understanding of different manufacturers’ systems.
Level playing field
If you specialise in a specific marque of vehicle, gaining the data shouldn’t be a problem as you can invest in the network tools and diagnostic access. While this can be expensive, it allows the workshop to stand on a level playing field with the main dealers. But where does this leave the general repair workshop?
As many workshops are set up around MOT bays that can’t turn a vehicle down just because it doesn’t have the right badge on the nose, they tend to repair all makes and models. That can get incredibly expensive with dealer-level software for all makes and models – not good when workshops are already being squeezed and the costs can quite easily run to more than a small workshop would earn in a year.
Another problem is that each manufacturer has a very different way of setting out data and software, making it tricky to both learn and jump between brands quickly, as is sometimes required
There are a few aftermarket solutions out there that do a good job of covering the basic settings and adjustments, but these can be vague with more in-depth component diagnostics, such as the expected outputs of a specific sensor. It’s also common to need at least two different aftermarket diagnostic machines to read most of the cars a workshop will see.
Even then there will be a few that can’t be read since there doesn’t appear to be one system that does it all. Even the more in-depth systems that carry more manufacturer data can be limited in the number of vehicles they cover, leaving the workshop completely blind when trying to work on a non-covered customer vehicle that rolls up to the workshop.
Electrical faults
With the rise of EVs, one issue is that manufacturers no longer consider components such as the high-voltage battery as repairable, so no data is supplied, even on the dealer network.
So what do you do when you have a possible cost of thousands to replace an entire battery when all it needs is a single cell replacing? It’s neither good for the customer or the environment, which is the whole idea behind EVs in the first place.
There needs to be a clearer path to access data, with the ever-increasing need for workshops and technicians to complete CPD and keep up to date with ever-evolving technologies. Asking a technician to diagnose issues on a vehicle when they don’t have the data just doesn’t make sense. Needing to know what good looks like is often an essential part of the diagnostic process.
None of this is very helpful to workshops right now, but it shows that businesses need to spend time researching the best tools for their business and investing funds to make sure they have access. It won’t be cheap and it’ll require unravelling a web of available data and tools, but it’s a cost that could be repaid with the increased number of vehicles you can work on.