Gazing into the future of battery management
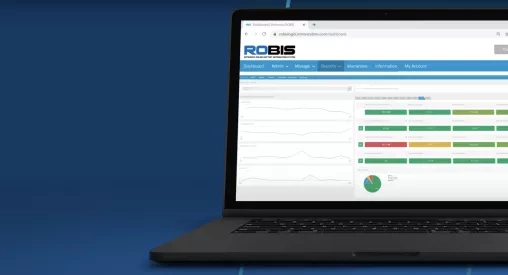
Advertorial: Trying to crystal ball the future is not everybody’s gift but trying to ensure that the equipment in any modern workshop is fit for the future should be. Battery technology is one area we should all be paying closer attention to.
Batteries are being used very differently in the present, especially if we look at how battery use has changed through the years. Because of that, we’re having to alter the way we test and charge batteries due to demand increases and additional loads.
Navigation, heated steering wheels and seats, de-misting options, in-vehicle entertainment, stop/start. The list of standard systems that come with any in-vehicle package is apparently endless and the batteries have a series of demands that are increasingly sophisticated.
But this increase in demand has not brought with it batteries that are double the size and coping ability. Even with performance improvements relating to AGM and EFB technologies, battery maintenance is critical to ward off failure, roadside defects, and costly avoidable problems.
Fleet of Foot
All workshops must be fleet of foot and able to cope with traditional combustion engines and, at the same time, look after EV and hybrid technologies. That means that the equipment to service this diverse range must accurately test and charge to be able to maintain vehicles optimally.
It’s important to measure not only the cranking ability but also the RC (Reserve Capacity) and we call this a process of conductance profiling. This means that a workshop can get greater accuracy of battery results and improved diagnostics.
Wireless-enabled software is required to provide leading-edge conductance profiling and charge acceptance testing. This means that any updates can be handled remotely, without breaking up workshop routines and service schedules. Only offering cranking amp analysis is not enough anymore as it is vital to understand the consumer loads.
So, what are the ideal technologies to help the modern workshop deal with the flexibility that is required to achieve accurate diagnostics.
Best Equipment
It’s really important to be able to give customers live information regarding their battery results and with the CPX900 Conductance Profiling™ Battery and System Analyser this means achieving a comprehensive health inspection. The CPX900 measures the existing reserve capacity and its cranking ability. Modern workshops conduct inspections every day and this provides Wi-Fi and Bluetooth connectivity, and all software upgrades are wireless. The CPX900 has full connectivity to the Rotronics ROBIS portal.
Being able to analyse the majority of batteries in under two minutes, and then provide a charge time that is within most service times, is an excellent feature of the DCA8000. The DCA8000, like the CPX900, also has wireless software updates and analytics.
The onset of electrification doesn’t change how important a battery is in a vehicle; there is no CCA element on electric vehicles and the 12V battery is still central for loading up consumer components. These 12V batteries will still require a full test and charge battery management programme to achieve optimal performance.
A bird’s eye view of a workshop team’s performance, or lack of, is really important and the CPX900 can help you do that as it will synchronise into ROBIS, Rotronics’ online portal. This will give managers an assessment of whether technicians are carrying out the correct test and charge procedures. From over 4.6 million tests gathered via ROBIS so far, we have identified that around 20% of those tests have inaccurate information entered. The main error culprits are the CCA of the battery or the type of battery and unfortunately the result is incorrect and that leads to remedial actions that are inappropriate.
What is ROBIS?
ROBIS is the first of its kind in the industry and is an online portal that gathers battery data following battery tests, to accurately assess what corrective action is required. This can all be completed remotely, and it is a bit like having an additional technician and a much-needed resource; like a digital analyst and low-cost technician who is on duty 24/7/365.
Our customers use ROBIS to help them problem-solve and achieve optimal performance form their fleet batteries or customers’ vehicle batteries. They also use ROBIS to assert consistency throughout the workshop and drive high management quality standards and workshop practices.
Developing a Battery Management Process
To be able to measure the health of batteries and gain accurate data to find the best solutions to battery issues within a workshop, there are a range of questions to answer.
- Will the tester do load testing?
- Will the tester measure reserve capacity?
- Do I know enough about charge acceptance?
- Is charge acceptance important in my diagnosis?
- What update options do I have for the latest battery technologies?