Get RC about battery management
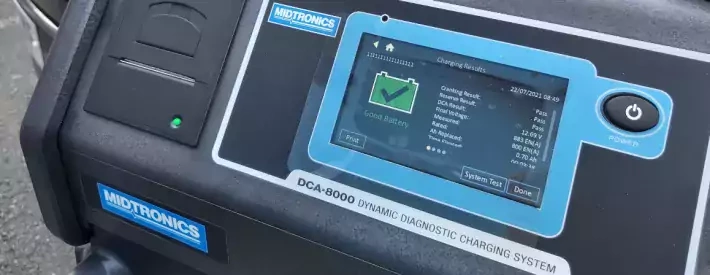
[Advertorial] Any business fleet of vans and cars will currently be a mix of combustion engine and electric, with a firm direction of travel towards becoming electric. Every new vehicle purchased will be EV. Cars and vans have a 2025 deadline to reduce CO2 emissions by 15% from the 2021 baseline and, by 2030, the target toughens to a 37.5% reduction for cars and a 31% reduction for vans. From 2030, no new petrol or diesel cars and vans can be sold and hybrid sales end in 2035.
At the time of writing, industry figures show that there are approximately 500,000 zero-emission battery electric vehicles on the UK's roads. There are around 400,000 plug-in hybrids. Automotive giants are making flagship commitments to the future of EV.
With this backdrop of change, all workshops will have to have battery management at the forefront of their activities; just because the battery is no longer used for cranking does not mean any reduction in care. A battery’s reserve capacity plays an important role in its ability to support the electrical systems, and this is the new battery management focus for workshops.
Ken Clark, Managing Director at Rotronics, the UK’s leading battery management specialists, shares his key considerations: “We must accept that these batteries have to be tested in a different way to determine their suitability for providing power for the vehicle. Now the key focus is on reserve capacity, as opposed to cranking ability, and increasingly charge acceptance. In the transition from ICE (combustion engine) to EV, it is critical to measure the reserve capacity of 12v batteries to make sure that the electrical system is fully supported.
“If your car/van fleet is transitioning over to EV there are some key questions that the workshop needs to be able to answer.”
- How and where will these vehicles be charged?
- Will they be charged at the business address or at the driver’s home?
- How will the batteries be maintained?
- How many miles will each vehicle be expected to do?
- Coming into Winter, the range reduces considerably. A 200-mile range can reduce to 120 miles
Clark continues: “In the winter months, there are some issues that significantly affect any car/van fleet.”
- Your drivers may need to be able to charge their vehicles more frequently as the range reduces, depending on the make and model, and the consumer loads that are going to be used in the day
- The 12v battery is vital to run the electrical system and cooler weather can mean a 50% dip in battery performance
- The technology is changing to suit the mix of ICE, PHEV, BEV, EV etc and you need to make sure that your workshop can maintain a range of batteries
Clark says: “We help our customers select the best technology options for them, according to their customer requirements or the mixed car and van fleet that they are responsible for.
“If I had an ideal checklist for any workshop to be able to maintain their vehicles’ batteries and achieve optimal performance, it would include the following simple steps.”
- Each vehicle that enters your workshop needs to be tested and charged
- Each bay needs to have test and charge technology
- Any batteries on the shelf need to be charged monthly
Clark says: “All of the Rotronics customers who follow these simple steps have the best performing batteries and the lowest rate of roadside defects.”
Check out the latest testing technology platforms, the CPX900 and the DCA8000, the PRO60 or the PRO120. And find out more about Rotronics testers and chargers