Is ‘gigapressing’ the new disruptor that will transform the skill set and operation of vehicle body shops
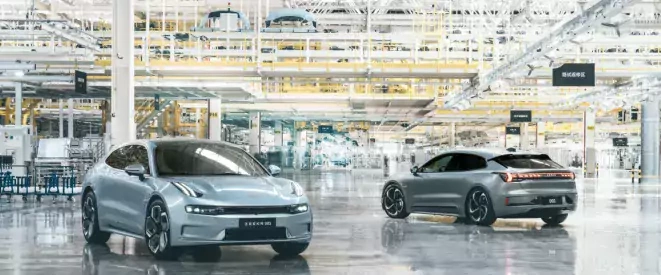
There are a number of car manufacturers who are joining Tesla in embracing the introduction of the use of massive aluminium die casts as a way of making the underbody sections and potentially other parts of the electric vehicles.
Geely’s EV brand Zeekr is the latest of a string of OEM’s that are turning to the use of ‘gigapress’ die casting. The concept is not new, metal and plastic die casting have been around for a number of years, but these have been concentrated primarily on smaller parts. The application to large aluminium underbodies in car making is relatively new.
The argument is that the technique eliminates the need for hundreds of welding points and in so doing cuts defects and makes the cars lighter while also improving structural stiffness. The other very persuasive argument put forward by the Chinese manufacturer is that it reduces manufacturing costs by 40%. In reality this type of development is still being developed and could easily move to other large sections of the car.
This type of breakthrough may help the manufacturer to produce cheaper cars but it presents certain challenges further down the supply chain. There have been a number of questions asked as to the repairability of these large parts of the vehicle. If the car is in a minor accident the replacement of a bumper would normally hopefully be sufficient. With a giga-cast vehicle it could entail a major repair including the replacement of an entire front or rear section.
This has a significant impact on body shop operations. These large sections can’t be repaired using conventional approaches. Once damaged it will require the local workshops having to deal with much larger parts requiring new different handling equipment and potentially different technologies. With these pressed items being introduced primarily in new EVs will there be a knock-on effect in potential battery damage as this will be sitting on the floor pan?
The further ramification is that if the issue of repairability is not addressed the potential for insurance premiums to rocket will inevitably follow. This could be a major stumbling block when customers way up the cost of ownership of EVs.
Zeekr are attempting to address the repairability issue by giving the ability to change select parts of the larger die cast section in the event of a collision. This however doesn’t give the same flexibility of repair that is currently available on cars.
Toyota has said that it is working on the ‘gigapress’ concept but with smaller interchangeable parts. The investment in the ‘gigapresses’ is large, and OEM’s will be striving to find commonality of parts across a range of their vehicles with the emphasis being on larger parts which deliver the biggest benefit in the cost of manufacture.
The aftersales side of the retail automotive business is going to be shaped by the move to EV with less moving parts and less cost in servicing the vehicles. However, the body shop of the future may also face significant changes in dealing with cars primarily formed by a ‘gigapress.’
Jim Saker is President of the Institute of the Motor Industry and Emeritus Professor of Retail Management at Loughborough University