How apprenticeships are adapting to the electric future
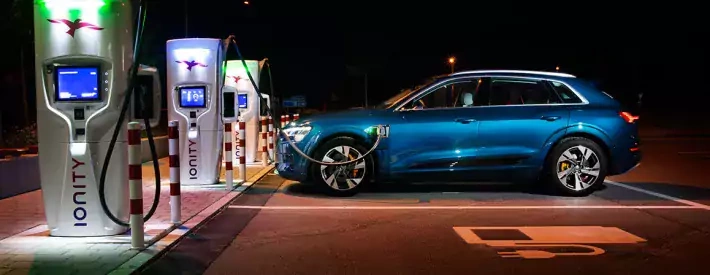
In this article: The move to electric vehicles and increased levels of connectivity will bring changes to apprenticeships, and could help make the industry more attractive
Apprentices are critical to the UK motor industry as it shifts to an electric future. This is because youngsters were raised around technology, and so possess innate digital skills that the sector’s ageing workforce can lack.
“Significant tranches of the labour force may be unemployable soon with the advent of electric cars,” says Mark Currie, CEO of training provider Mantra Learning.
“Few UK cars are electric now, but this sum could rise substantially soon.” The incoming tax change, when pure electric company cars will be benefit-in-kind tax free for 2020, “is a massive catalyst to make everyone move to electric cars”, he says.
Apprentices have long been a key talent pipeline for the motor industry, which hires 12,500 of them each year. Apprentices will have traditionally gotten their hands dirty changing tyres or rebuilding engines, but increasingly, they are learning digital skills on computers, including coding.
Apprenticeships are adapting to a digital revolution in motoring, adding training requirements for alternative fuel systems, including electric and hybrid technology, for technician roles in the UK. This includes the motor vehicle service and maintenance technician programme that was created by Jaguar Land Rover, Mercedes-Benz, BMW and other employers.
Some apprenticeships also include electric and hybrid technology qualifications, but only a minority of technicians are qualified to work on these cars, even though demand for electric vehicles is expected to surge.
Mark Armitage at the Institute of the Motor Industry describes the new requirements and qualifications as “a massive step forward”, but adds “there is still more to be done”.
For example, he says obtaining electric vehicle qualifications is not yet a mandatory requirement for apprentices. And only a few programmes test apprentices on their knowledge of hybrid and electric fuel systems as part of an “end point assessment”.
“Some vehicle manufacturers, such as Tesla, do not have conventional combustion engines in their line-up, meaning many apprenticeships do not meet their business requirements,” says Armitage.
A new “trailblazer” group of employers could be formed to accommodate the rapid introduction of electric vehicles in the UK, he says. Trailblazers develop apprenticeship standards that state the skills, knowledge and behaviours that apprentices should obtain.
Sally Gilson, head of skills at the Freight Transport Association (FTA), agrees that “new apprenticeships will need to be developed as demand for different technologies increases”.
Technology goes beyond technicians, she says. Haulage firms need advanced telematic systems to manage their fleets more efficiently, and safety systems to keep drivers safe.
Warehousing is also changing because of technology. The growth of online shopping has led to the automation of the picking and packing process within warehouses, which has reduced costs.
Although there is anxiety around automation, the FTA’s latest skills reports says, “in reality, technology is still limited in what it can do and is transforming job tasks, rather than eradicating occupations”.
Gilson says that “as a sector, we need to be ready for those training needs”, but adds that apprenticeships are unlikely to fit all of these needs because they are so varied.
However, Currie says that apprenticeships will definitely bring crucial technology talent into the motor industry, since the programmes attract young people.
“The fact that the cars have made this transition to an electric future has helped with the sector’s image,” he says. “In the past, trucking was seen as a dirty, horrible, greasy, slimy job. Technology has made it cool again.”