How to manage difficult testers
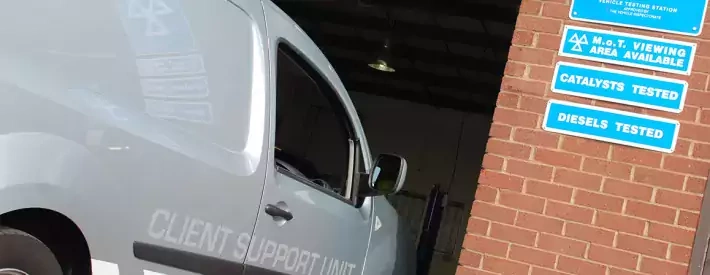
In this article: Managing MOT testers, like anyone, can be difficult at times, we look at how to deal with those who aren’t necessarily working to the rules
I was asked by a garage proprietor to investigate a tester who was causing friction in the workshop. If another technician serviced or worked on the brakes of a vehicle before his MOT test, the test would invariably result in a fail. He also had a disproportionally high failure rate for brakes.
The tester thought he was in a strong position as he was the only qualified MOT tester within the business. I asked the proprietor to have a low mileage 3-4-year-old car serviced last thing by a different technician on the Saturday and be tested first thing Monday morning.
Finding the cause
I arrived at ten o’clock and retested the (not surprisingly failed) car. The brakes passed my test with ease; the front brake pads were worn to 2.5mm – well within the 1.5mm point of failure. The vehicle had apparently been failed for imbalance across the front brakes. What the tester had done was alter the nearside reading by knocking off 100kg of effort. My test on the roller brake tester (RBT) revealed no imbalance at all.
I questioned the Tester, who was adamant that the readings he had entered onto the MOT Testing Service were those obtained on the RBT. He was unaware that the RBT stored all the results, so I could find his earlier test and the results generated. The tester became agitated, but stood his ground, so I started to look at his earlier tests and at that point he confessed to what he was doing.
When he found worn but passable brakes, he tipped them into a failure by way of imbalance – he justified this by claiming that 2.5mm was not enough pad material to be safe, so was doing it for road safety. However, he could not find a reason why he regularly failed cars that had just been serviced by his colleges.
This substandard testing was being conducted in a well-run garage. Thankfully the garage owner was prepared to act herself rather than shrug her shoulders or wait for the DVSA to find the problem. And that’s the important thing – being proactive. For reasons I don’t understand, some garage managers take the attitude that they’re not a tester so can’t possibly intervene. Wrong.
Step in
Intervention is a managerial necessity. While only the MOT tester who registers the test has the powered to pass or fail it, the authorised examiner is rightly expected to monitor test quality, results and conduct audits. What was conducted here was part quality control, (standard of test result), and part audit, (examining stored brake test information).
Generally, a quality control failure would not cause a garage to notify the DVSA. The MOT Testing Guide states that: “The key thing here is to show that corrective action is taken.” This corrective action is usually in house; if you’re confident that the tester has learnt from their mistakes and that the shortcomings found are unlikely to happen again then that’s satisfactory resolution, but you’d expect to increase your quality control process to ensure the improvement is permanent.
In this example though it seemed the tester was entering spurious and false information onto the testing service, which brought his honesty into question. I therefore recommended that the authorised examiner should inform the DVSA of the findings.
Managers shouldn’t be scared or reluctant to take positive steps to improve the quality of the service they provide, even if it means confronting staff who could be causing, to put it politely, mischief.