How technology could ease the skills shortage
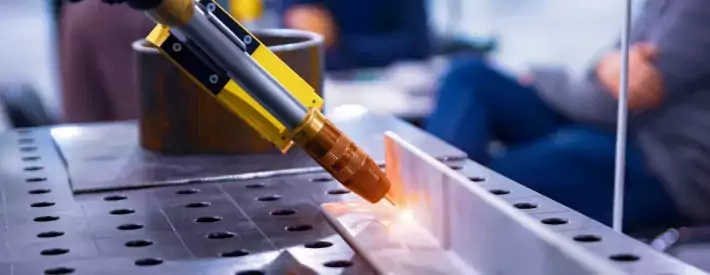
There’s a pressing challenge that’s becoming increasingly apparent across various industries – a shortage of skilled workers. This predicament has permeated discussions and is a growing concern for businesses worldwide. Attributable to a multitude of challenges from the aftermath of Brexit, or flaws in the education system, the shortage of skilled individuals is a formidable issue that needs attention.
Opinions on the root causes of shortages vary, but it’s evident that the automotive industry is particularly hard-hit. Technological advancements, occurring at an exponential rate are a significant factor exacerbating this situation. Over the next decade, the automotive sector is poised to witness as many innovations as it has in the past century.
It all makes for a formidable challenge in training individuals to bridge the growing skills gap. Compounding this issue is the time-intensive process of developing qualifications, potentially reaching a point where technology advances faster than individuals can be adequately trained.
In the early stages of the automotive industry, from the inception of the car until the mid-90s, technological changes occurred gradually. Technicians could easily keep pace by sharing knowledge with colleagues and attending occasional training events. However, with the widespread adoption of injection technology, the landscape shifted dramatically. The proliferation of complex ECUs and Advanced Driver Assistance Systems has made it increasingly difficult for Technicians to stay abreast of advancements. Finding trustworthy and skilled staff has become a monumental challenge for businesses within the automotive sector.
It’s impacting everyone
The challenges faced by the automotive industry are not isolated; the welding sector grapples with similar issues. In response to the shortage of skilled welders, there are some innovative solutions being explored. Notably, the utilisation of robots for welding tasks emerging as a potential remedy.
Once constructed and programmed, these robots only require a Fire Watcher to operate, enabling them to work around the clock if there is a continuous workflow. The training required for a Fire Watcher is comparatively simple, and one individual can oversee multiple robots simultaneously. While robots may not currently service vehicles, the prospect of such technological advancements remains open for exploration.
Considering the trajectory of technological evolution, there may be more effective ways to integrate technology to alleviate the burden on Technicians. Rather than completely replacing human roles, technology could be harnessed to divide tasks and support technicians in their work. By strategically incorporating automation and artificial intelligence, businesses can enhance efficiency without compromising the need for human expertise and judgment.
It isn’t about replacing people
The adoption of technology in addressing the skills shortage is not about replacing the workforce; it's about empowering and augmenting it. Collaborative efforts between humans and machines can pave the way for a more sustainable and resilient workforce. Embracing technological solutions could be the key to navigating the challenges posed by the skills shortage and staying competitive in an era of rapid technological advancement.
Another potential solution involves taking a more holistic approach to staff training, focusing on equipping individuals with the skills needed for the future. While this approach may not be universally popular, as it could limit freedom of choice for many, it offers a proactive response to the evolving demands of the job market.
The automotive industry may witness a significant shift away from a one-size-fits-all technician model, with the workforce specialising in smaller, more specific areas. This change could reshape how aftermarket workshops operate, potentially requiring more staff to cover a diverse range of tasks. This could possibly see the end to the “Fred in the Shed” style workshops and see a greater rise in the multi branch independents, or could swing the other way and see a rise in smaller independents that just specialise in one area and collaborating with other workshops more and more within an independent network.
The skills shortage is a growing issue affecting industries globally, and the automotive sector is no exceptions. Technological advancements, while contributing to the shortage, also present opportunities for innovative solutions. By leveraging technology strategically and fostering collaboration between humans and machines, businesses can not only address the skills gap but also position themselves for success in a dynamic and rapidly evolving landscape.