The member view: The future of vehicle repair
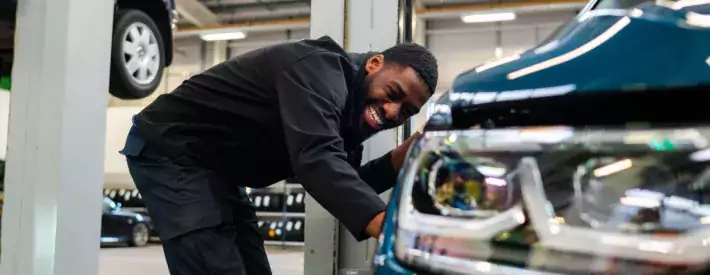
The future is electrified, driven by a mix of politics and taxation, but how will it change the vehicle servicing and repair sector?
Hybrids (MHEV and HEVs), plug-in hybrids (PHEV) and battery electric vehicles (BEV) all have regenerative braking, so the service brakes may not do any work during routine-check braking or slow deceleration. This will lead to a reduction in brake pad and disc replacement volumes at 30% of the rate of an internal combustion engine powered vehicle. This has already been modelled and verified by many large OEMs over the past decade. Furthermore, we can see the re-birth of the drum brake on rear wheels, since BEVs in particular don’t need the same massive power in the braking system as ICE vehicles.
Of course, even a BEV uses oil, and the next generation of BEVs is likely to follow static high-voltage systems by using oil as the primary coolant. For the moment, oil is used for the transmission, which takes quite a beating due to the electric drive system’s high-peak torque from stand-still. Even so, over the next three years we can expect (as the vehicle parc gains a greater population of BEVs) that oil change volumes will start to fall.
Indeed, traditional service work for internal combustion engines (although likely to be dominant until at least 2035) will reduce for timing drive systems, spark plug changes, glow plug changes, fuel injection systems, and oil changes. Overall, I would expect a 10% reduction in this work by 2028.
There are positive changes due to the transition to an electric future. The humble BEV has a powertrain that can drive the vehicle up to just over 100mph; the way it gets there is thanks to the mountain of instant torque more akin to a BMW M2. Early adopters of BEVs have indulged this performance, meaning by year three of ownership the vehicle is more likely to have distressed suspension bushes, emotionally challenged wheel bearings, and above average damage to suspension links.
The cooling systems are a moving feast. BEVs, PHEVs and now some HEVs use more than one cooling system on the vehicle, and all feature both an electric driven AC compressor, as well as multiple electric coolant pumps. Heat pumps and on-board solar panel charging are also available, adding to the complexity of the HVAC systems, especially on BEVs; heating is also provided via the seats, steering wheel, as well as an electrically-powered heater unit inside the HVAC module. Put simply, cooling system complexity extends way beyond the traction battery, traction motor, and power controller – and is still evolving, hence the move to oil-based systems.
The first-generation Nissan Leaf is an interesting case study. We now know that the traction battery cooling system was inadequate, but was re-engineered several times to address the loss of battery life. This also included keeping the traction battery warm during cold days. Nissan moved through at least three powertrain iterations between 2010 and 2017 before completely replacing the model. Now that first generation lives on via specialist repairers.
This is just a quick look at what’s to come as electrification rapidly evolves and the skills needed to work on vehicles changes as the industry evolves.