On the MOVE: why skills are critical to the future mobility debate
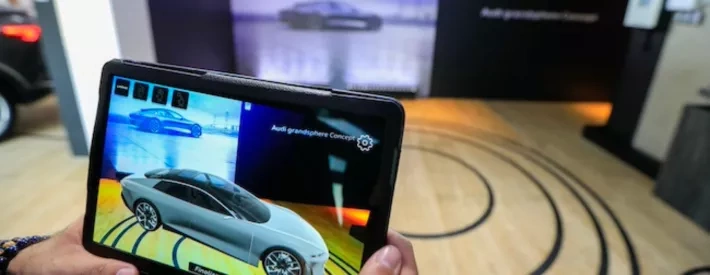
IMI CEO Steve Nash was part of one of the high-profile panel discussion on skills. “MOVE has become a key annual event,” he says. “Run over a couple of days, and centred around electrified vehicles, it's a showcase for everything to do with mobility – from micro right up to huge hydrogen trucks.
Nash formed part of the Auto manufacturing and skills: reshaping the industry in the electric image session. Moderated by George Galliers, Head of European Automotive Investment Research at Goldman Sachs, and featuring Anne Fenninger, Head of the Data & Software Academy at Stellantis, and Oana Penu, Skills Institute Director at EIT InnoEnergy.
“The other panellists represented vehicle manufacturers and Tier One suppliers, so it was important to complete the debate,” says Nash. “Obviously you need an appropriately skilled workforce to build EVs, and then an appropriately skilled workforce to sell, service and support them. It’s a symbiotic relationship and here in the UK three quarters of the workforce operate outside the factory gates.”
There are a lot of challenges that need to be met; skills issues posed by electrification is just one. According to the Automobile Manufacturers' Association, the industry directly or indirectly employs close to 7% of the EU workforce, so this is a massive issue.
“When it comes to high-voltage, safety is paramount. There are new skills and regulations different to those for internal combustion engines. There are other new technologies too – the whole connected, autonomous, shared and electric piece – plus hydrogen,” says Nash.
Through IMI TechSafe, the institute’s suite of skills solutions for new technologies, it’s been successful in getting the UK government to focus on what happens outside the factory gates, the part of the equation that tends to get overlooked.
Nash says: “We’ve gained government recognition, and endorsement when necessary, and influenced vital legislation, like the skills element of the Automated Vehicles Act.
“We're also operating in other countries, to support international qualifications and promote the standards we've established here. Our TechSafe solutions are in huge demand, including in China. They have amazing EV products, but they don’t have the workforce outside the factory gates to look after them. They need to train something like 11 million people, which is mindboggling.”
Training and upskilling is an incredibly important issue closer to home too.
“From an upskilling perspective, the ban on sales of new petrol and diesel cars slipping from 2030 to 2035 was not helpful. We had already worked out that we needed north of 100,000 people to be appropriately EV qualified by 2030. Then the government flipflopped. We're still moving forwards on upskilling, but we've seen the run rate slow because more people are thinking that might even take me beyond the end of my career,” says Nash.
“At the same time, we have the new Zero Emissions Vehicle mandate, which is causing all manner of market distortions. Some manufacturers are looking at reducing non-electric sales to meet the targets. There are predictions it could drive new sales down as low as 1.3million. It’s a nonsense.
It’s a mix of issues that is putting pressure on the ever present skills gap in the industry, but there is some good news – although admittedly there’s till a lot of work to be done.
“We came out of the pandemic with 24,000 vacancies across the industry in the UK. Via a combination of bringing in new skills, and developing the existing workforce, we've got that down to 22,00. We’re making progress but there’s much more to do.”