Tread carefully: how tyre technology is evolving in an EV-era
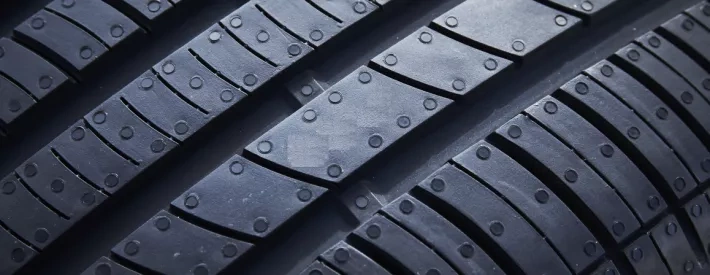
IMI research shows that electric vehicle tyres suffer higher levels of wear thanks to the added weight, but what are tyre manufacturers doing to solve the problem?
According to analysis by the IMI and Garage Industry Trends, tyres are the weakest link when it comes to MOTs. This makes them the greatest risk to road safety should the government’s proposed extension to the first MOT date get the go-ahead.
Thankfully, the message from the industry has been unified in its objection, so hopefully the extension won’t happen, but what exactly is the issue with EV tyres?
The EV challenge
Put simply, electric vehicles tyres experience more wear than those for ICE vehicles. Comparing like for like, EVs are heavier than regular combustion engine vehicles thanks to the extra technology under the bonnet.
“EVs tend to have higher torque at a lower speed,” explains Jaap Leendertse, General Manager of PCR and SUV tyre development at Falken Tyres. “The advantage normal combustion vehicles have is that they actually have a low torque at lower speeds. So even from 0-1mph you are already stressing out the tyre.”
It’s a known issue in the industry and tyre companies such as Falken are working hard to lessen the impact.
“We have done a lot of work on our EV-specific tyres,” says Leendertse. “We’re making constructions that can carry more weight. The tyre pattern is designed so that during rolling it leaves some flexibility, resulting in no immediate abrasion. The pattern is then a bit slower, meaning it doesn’t react as fast under braking.
“The compounds are very particularly designed,” he continues. “We’re designing them to avoid faster wear. It’s also the biggest difficulty since you need a better balance between efficiency, performance and durability for EV tyres compared to tyres for combustion engines.”
Balancing act
Maintaining the key attributes of a tyre found in a combustion engine vehicle but in an EV is a balancing act for tyre developers. They need to add increased durability as well as other attributes that are specific to electrified vehicles, including lowering road noise.
“A normal tyre needs a little bit of flexibility,” says Leendertse. “But if we give the same level of flexibility to an EV tyre, we have a problem because it’s wearing out too quickly due to the much larger weight. Noise is a higher priority. There’s no engine noise so tyre noise is amplified, and that’s something we’re working on decreasing. Aerodynamics are another big factor.”
While IMI analysis has shown that EV tyre technology isn’t yet at the level it needs to be, Leendertse is excited about the opportunities to find the improvementsneeded, as well as how approaches can take a different direction as previous problems become less of an issue.
“The future of EVs is certainly very interesting,” he says. “In the past we’ve had new models, but most of the time the tyre sizes are relatively the same or just have a small change. With EVs, you have so much more weight and torque to contend with, which means the whole tyre is different.
“We don’t have to care too much about the hydroplaning anymore, since the increased weight means that the water will escape automatically. And you have totally different dimensions – a higher size than before. We have to completely change our line-up, whereas in the past, we were just fine-tuning. That will change again in the next five or six years, and every year we will come up with something new. Ultimately, it’s about getting the tyre to carry that weight safely without the wear.”
Assessing tyre wear
Alongside Falken’s tyre research and development work, a joint project between Falken’s parent company Sumitomo Rubber Industries and Kansai University, Japan has resulted in the development of a brand new power generator that measures the exact amount of wear a tyre has.
The generator uses a tyre’s rotation to generate electricity and supply power to peripheral sensors installed in the tyre without relying on batteries. This ‘Miniature Energy Harvester’ is a sustainable technique to measure tyre wear, enabling the calculation of a tyre’s contact patch and wheel rotations while recording stress levels based on the amplitude changes induced by the rotation of the tyre.
The information gained by the system could help the development of tyres in the future, allowing manufacturers to develop technologies that enable better quality tyres that offer decreased wear and increase safety for vehicles, drivers and passengers.
There are still few legitimate reasons to change the MOT requirements, and no matter what happens to EV tyre design, that’s unlikely to change. But improvements to what is a vehicle’s only contact point with the road will always be welcomed.