Why electric vehicle charging can go wrong and how it's being improved
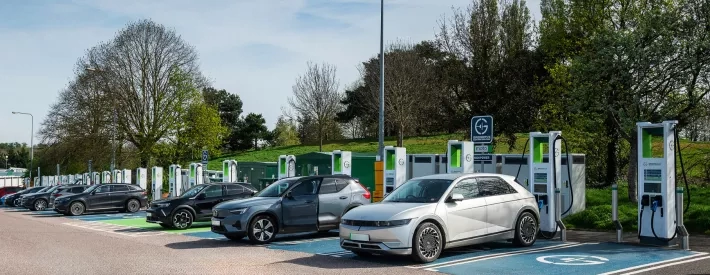
Not many people think about pump issues when they pull up at a garage to refuel a petrol of diesel vehicle. There are problems with pumps being out of order, but as we’ve become so used to the process we rarely even acknowledge it happens.
The same can’t be said for EV chargers. If there’s any downtime of the infrastructure it can make headlines. More importantly it can also cause real issues for users; family getaways become even more stressful, business trips take longer than they should and commercial fleets end up with unnecessary (and expensive) downtime.
The sector is improving the infrastructure and there’s concerted effort to make charging an EV as pain-free as possible with a targeted first-time success rate of 100%. Gridserve is one of the firms working hard to make sure the infrastructure works for everyone.
It currently has over 190 locations across the UK, with over 1,400 charging bays and 200,000 charging sessions a month.
It’s a complicated business
There are enormous differences between recharging an EV and refuelling a combustion car, which makes the infrastructure comparison perhaps a little unfair.
“The hardware of a petrol pump is much simpler than an EV charger. There's no interaction with the vehicle at all, there's just a user who puts a hose in a hole, basically,” says Pete Bishop, Chief Technology Officer at Gridserve. “The amount of comms that has to go on between the charger and the vehicle to get to the point where you can put energy into the vehicle is incredibly complex. It can go wrong in many ways.”
Bishop and everyone at its Innovations and Operations Centre is working to get to the vision of a first-time success rate of 100%. It's some way from that at the moment and Bishop says for Gridserve it’s probably at around 70%. But work is ongoing and he’s confident improvements could come very soon.
“We've identified quite a few of the contributing factors to that I could see we can probably get 10% to 20% better in the next six months when all those fixes come through,” he says.
What are the challenges?
There are a huge number of linked systems in a vehicle charging station, and if customers want to be able to turn up and charge none of them can have a fault.
“First we've got to have power on the site, then we've got to have comms. Then we've got to have the charger itself working. Then we've got to have the back office software for the charger working. Then we've got to have the connectivity with the bank [working],” says Bishop.
A fault in any of those areas will make the charger unavailable. There are other issues too; chargers are environmentally impacted as well. But improvements are coming.
“It's thermally cycled every time you use it because it heats up, cools down, all puts a lot of stress on the electronics. We're seeing incremental improvement in the hardware reliability of the products. We're also working through a lot of software issues. We've had historically software issues that would make the charger unavailable that can actually be fixed by rebooting, resetting, or reconfiguring,” says Bishop.
The chargers are also capable of detecting issues and allowing preventative maintenance to happen, getting there before they fail rather than after they fail.
Of course there are other reasons why charging sessions fail and it has nothing to do with the hardware or software. People have a knack of making mistakes.
It could be as simple as not following the instructions correctly. Tapping the payment terminal before plugging the car in, or maybe not plugging in correctly in the first place for example.
Work is ongoing. The charging infrastructure is new, but expanding and improving, well on the way to making sure that no matter what vehicle turns up – passenger car, van or HGV (yes they’re coming, with 500kWh batteries and using high-power charging stations) – they can plug in and charge first time of asking.