Why Kia is supercharging its approach to developing industry skills
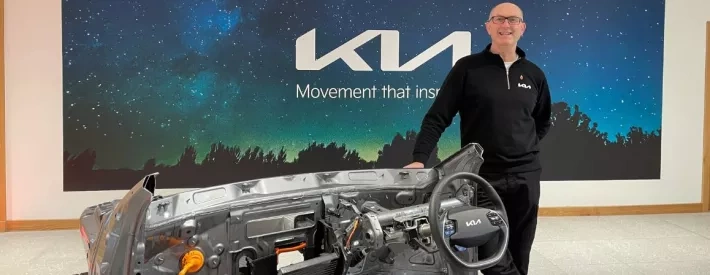
With so many technological changes in the industry – electrification, ADAS and connectivity – it’s important to make sure the sector’s people are ready. It’s a challenge even the biggest names in automotive are facing, and thankfully many are shifting their focus more intently on skills to help maintain their success.
Kia has invested heavily in its state-of-the-art training centre – the Kia Academy – to make sure that its people’s skills keep pace with the changes happening across the industry.
Kia is collaborating with Skillnet to train around 250-300 apprentices per year, nurturing their expertise in the latest automotive technologies and customer service techniques. As well as the home for the Kia Apprenticeship programme, the Derby site will serve as the hub for adult technical training for the entire UK Kia network, bringing the delegate number to around 1,500 per annum.
“The whole environment is conducive for learning. The equipment we have is in keeping with what dealers should have, so they're not seeing anything different. Everything we train, everything that we expose them [learners], they can actually benefit and actually impart that when they're back at work,” says Mark Godson, Technical Training Manager at the Kia Academy.
Kia’s new facilities opened at the beginning of the year, and as an IMI approved centre offer a range of courses and qualifications including Level 3 EV courses, it’s also approved to deliver Level 4 too with the Godson ready to welcome learners into the academy well into the first quarter of 2025.
The training programmes are continually developing, and Godson and his team always have one eye on the future to make sure that people coming through the academy’s doors are ready for whatever comes next.
“They have to continually develop because the technology on the cars is continually changing. The [Kia] EV3 has a different HVAC system which we've not seen in Kia models. So that now forms part of the HVAC course. If we look at the EV9, our halo model, it's absolutely brimming with technology. It has the latest ADAS fitted, and obviously the electrification as well,” he says.
So, moving forward whenever Kia launches a new vehicle, the embedded technologies will change the academy’s course requirements so it can match the needs of those working on them in the workshop.
Looking to the future
The Kia Academy isn’t just about maintaining and building skills of people already in the company. It places a huge emphasis on making sure there is a constant flow of new talent coming through its doors too.
The Kia Apprenticeship programme is run in partnership with Skillnet and uses a bespoke approach that focuses on education in electrification. Important considering Kia’s commitment to electrifying its fleet.
Kia offers three different apprenticeships: Light Vehicle Technician, Service Advisor and Combined Service and Parts Advisor. The light vehicle pathway involved the largest number of students.
“We have 208 apprentices on the programme at this moment, 167 of those are third years coming to the end of their studies,” says Godson.
That means its nearly time for them to take their end point assessment (EPA), something that could prove a stressful time, but Kia and Skillnet are trying to minimise the worry and help apprentices through this final hurdle. The first part of that is simple; making sure apprentices are aware of what’s coming so there are no surprises.
“Towards the final blocks of their third year Skillnet start recreating the [process] with mock EPAs, so it doesn't come up to them in like out of the blue,” says Godson.
It sounds logical, but it’s important for apprentices not to be thrown into the deep end. But it also feeds into the assessment environment too. When Kia apprentices run through mock EPAs, they set up the workshop in the same way for the actual assessment. It just means that apprentices know exactly what to expect.
“When they do come to do the EPA, hopefully we've allayed any fears that the apprentices may have, because they do put themselves under a lot of pressure and that's when mistakes happen,” says Godson.
Kia’s apprentices will use the same workshop, the same car, the same tools so there's a lot of familiarity. The one thing that won’t be familiar is the assessor. “They don't stand over them, they're watching from afar,” says Godson.
And so far, things have gone well for the students going through their EPAs.
“We've had some really good results. I think we've only had one failure from a practical assessment of which we spent time with that individual to find out why that may have been,” says Godson.
Filling the void
With students coming to the end of their studies attention turns to bringing in the next cohort of apprentices. And the signs are positive, with more seeing the benefit of skilling a new generation of talent.
“We're doing a tremendous job in terms recruiting and replacing the third-year apprentices. And we're now getting dealers on board to have more than one apprentice because they realise that the only way to fulfil their budget requirements from a service management perspective is to increase technician [numbers],” says Godson.
Godson and his team at the Kia Academy are continuously looking at how to improve the curriculum, expand the courses and qualifications on offer, and make sure people are passing the assessments. It’s critical to Kia’s future success but is also an example of why every business in the industry needs to pay greater attention to skills if they want to be successful.
Check out how the IMI could supercharge your career with its range of courses, qualifications and accreditations.