Demystifying automatic transmissions
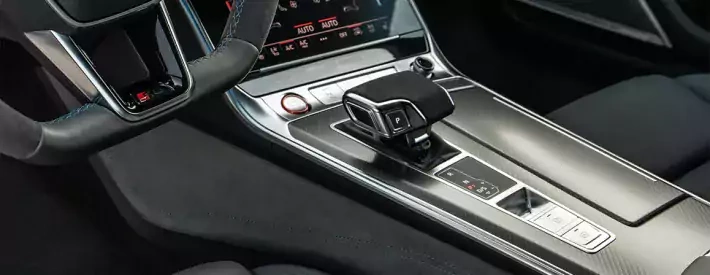
Automatic transmissions are becoming increasingly popular, so when one comes into the workshop what do you need to look out for?
Automatics have long been the go to transmission in the US, and now the technology is increasing in popularity on the other side of the pond too.
Ford reported that the number of cars equipped with automatic transmissions sold in Europe has tripled in the last three years – increasing from 10% of sales volume in 2017 to over 31% in the 2020 calendar year.
It seems like an obvious choice as an automatic removes some of the stress of driving, especially as roads become busier and more congested. But unlike a manual transmission, they do add complexity to the vehicle.
Instead of the driver selecting the desired gear, an automatic transmission uses a number of sensors to gauge when the shift needs to happen. These sensors feed data into the powertrain control module and transmission control module and create an overall picture which is sued to gauge when to change gears.
So, what are the key components and what are the key things to look out for in the workshop when faults arise?
Input and output speed sensor
The input shaft speed sensor (ISS) measures the RPM of the input shaft while the output shaft speed sensor (OSS) measures the output shaft. These two sensors work in tandem to help the powertrain control module calculate the speed difference between the engine crankshaft and transmission output shaft and hence the gear ratio. Given the importance of these sensors the EOBD standard contains DTCs for both the input and output speed shaft censors. For example, P0723 indicates an intermittent circuit for the OSS, with the likely cause being a wiring fault or poor connection to the PCM.
Throttle position sensor
The throttle position or TPS is typically located on the shaft of the throttle plate and directly monitors the position of the throttle – in modern cars this will be a non-contact sensor, which may use the Hall effect or induction to monitor the resistance between the moving magnet and a sensor mounted within the gearbox cover.
Turbine speed shaft sensor
The turbine speed shaft sensor generally consists of a coil wrapped around a permanent magnet – when a magnetic material moves through the field created by the permanent magnet, it changes the field lines, inducing current in the coil, reversing direction as the material moves towards the fields and then away – in other words, generating AC voltage. The amplitude and frequency of the voltage generated corresponds to the speed of the turbine and the distance between the sensor and the turbine.
Coolant temperature sensor
The fuel management system uses the coolant temperature sensor to detect the engine’s operating temperature; the PCM also uses this sensor to regulate the air fuel mix and regulate the clutch. As with the IAT, the coolant temperature sensor is measuring voltage; the resistance of the sensor changes based on the temperature.
Airflow sensor
The PCM uses readings from the airflow sensor to determine how fast air is moving into the engine intake. Hot-wire airflow sensors (mass airflow sensor or MAF) are the most common in modern vehicles and constitute a heated filament and a temperature sensor – when the engine is idling it takes very little current to keep the wire hot; when the throttle opens, air flows over the hot wire, cooling it; the more air flowing through, the more current needed to keep the wire hot. A volume airflow sensor (VAF) uses an air vane with a spring attached to a variable resistor. As the angle of the air vane changes due to the drag force of the air moving through the intake, the voltage measured changes.
Issues with the airflow sensor may be recorded as a powertrain trouble code – for example, P0102 indicates low input from a MAF or VAF with the probable cause being a wiring short to earth.
Once the PCM has determined a gear shift is needed, the torque converter comes into play. The torque converter comprises the impeller, which is attached to the crankshaft, and a turbine, attached to the input shaft of the transmission. The torque converter is filled with transmission fluid; as the impeller turns it moves the transmission fluid which in turn moves the turbine – this is called fluid coupling. The stator sits in the middle of the connector and regulates the movement of the transmission fluid. At high speeds a lock-up converter mechanically connects the engine to the transmission input shaft, leading to a 1:1 drive ratio. When changing gears this disconnects, decoupling the engine. Once power has been transferred to the input shaft, the planetary gearset meshes the correct combination of gears via small friction clutches, actuated by transmission fluid pressure.