Helping training providers go EV
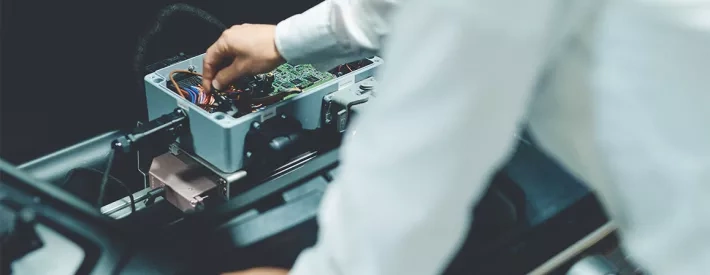
We’re facing an electric future from 2030 onwards. Training providers will have to invest in new facilities to upskill technicians. But fear not – help is on hand in the form of the Local Enterprise Partnerships
It’s clear that the future of automotive is electric. The UK government has well and truly set that ball rolling by confirming that new petrol and diesel car and van sales will be banned from 2030. So, while sales of EVs might be relatively low for now, increasing consumer demand and the huge number of new electric models hitting the market over the next few years will drive a massive shift by the time that deadline rolls around.
Along with greater use will come greater demand for technicians capable of servicing EVs. The industry needs to ensure there are enough of them trained up and ready to do the work, which means employers need to start thinking about electrifying their skills base. Thankfully, preparations are already under way.
For one thing, training providers are gearing up. A total of 136 IMI-approved training centres currently offer EV solutions. However, according to Steve Scofield, the IMI’s Head of Business Development, that figure falls a long way short of what’s needed.
“It’s incumbent on the IMI to try and generate interest and keep centres moving forward with their staff and their EV capability, whether that’s workshops, software, staff skills or qualifications,” he says. “All those who offer apprenticeships or full-time training for learners in automotive, if they don’t do this, they won’t be around in the future. It’s about the network of training providers staying relevant, supporting the sector and even helping to get the message out there, because they’ll be in touch with local employers who aren’t aware of the pace of change. The skills gap here is absolutely huge.”
One way the IMI is helping to move the dial on EV training is by working with the 38 Local Enterprise Partnerships (LEPs) across the country, which exist to help local businesses thrive and grow.
The IMI first got involved after receiving a call for help from Basingstoke College of Technology (BCoT). As Scofield explains: “BCoT was keen to get involved with EVs but didn’t really know how to go about it. Luckily, there was a chance that they could work with the nearby LEP. The college wanted to repurpose some old premises, make it all state-of-the-art and put in some high-end training equipment, so we gave them the steer about how to get to that.”
BCoT also needed help putting a bid together for LEP funding to help with the project. The IMI had the expertise and knowledge around EV training, development, certification and qualifications, so Scofield and his team helped to put the bid together, backed up by a business plan.
Now that everyone’s listening…
The experience with BCoT has led to the IMI working more closely with the national LEP Network.
“Prior to lockdown, I presented in London to the LEP Network Skills Leads about the pan-sector challenge. They didn’t have a clue it even existed,” says Scofield. “All of a sudden, the LEPs are awake to the issue of transitioning to EVs. Thankfully, the senior management in some of the further education colleges weren’t furloughed and have been planning while we’ve been in lockdown, working with my team and the LEPs.”
Following the model used by BCoT, to date, three centres have been able to access LEP funding, and a further six are in the pipeline to do the same. Scofield sees the link with the LEPs as a crucial connection with national skills training. “The LEPs themselves are exceptionally well connected. For example, the LEP Network’s Chair and CEO recently met with the Chancellor, Rishi Sunak,” he says. “That’s how connected they are to government policy around skills.”
Beyond acting as a source of funding for training providers looking to make the switch to electric, the LEPs will also help to make that change stick. “The good thing about the LEPs is that they’re helping the initial transition. Once the business case stacks up, it’s the full-cost training provision that keeps it sustainable,” Scofield explains.