How 3D Printing could revolutionise the aftermarket
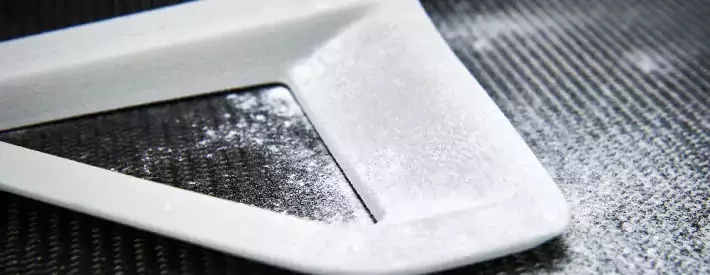
The 3D printing industry has boomed in the last 10 years from a niche community to a global industry creeping into every corner of the world. As we face both environmental and cost concerns, it’s a technology that could well begin entering the workshop allowing short, cost effective runs of parts.
We’ve already used the technology to overcome challenges in our business, proving that there is real world applications for 3D printing.
A simple fault can render a car unroadworthy, and this was certainly the case for a troubled Chrysler Ypsilon that presented to our workshop with inoperable wipers. A long-term customer with a well-maintained car for a fairly run of the mill repair, initially it was booked as an ideal job for the newly employed apprentice who was keen to fix something.
Initial examination didn’t produce any surprises, the steel wiper arm had worn through the plastic housing which caused the linkage to jam up on the motor. As the plastic part is integrated into the motor, a whole new wiper motor and linkage is required to fix the issue. That in itself isn’t a massive problem, but it’s costly for the motorist. The part was ordered and was expected within a couple of weeks. Then another couple of weeks, then another – then after six weeks the motorist was understandably becoming concerned, and the car was becoming a lump sat in the workshop not earning any money. Chasing the manufacturer was fruitless and to this day there is still no idea when the part will become available.
A new approach
Writing the vehicle off seemed excessive, having a history in fabrication and an interest in modern methods, I’d already invested in a fairly cheap 3D printer, and this seemed the ideal opportunity to try and find a solution that was foiling the dealership network.
The 3D printed bush was quickly designed and produced, using the £150 printer, and around £0.20 of filament. That said the process would have been far more efficient if the original file was accessible instead of needing to reverse engineer a solution in CAD. The motorist has paid a deposit for the part from the dealership, and it’s hoped the temporary fix will get her through until it arrives, but with the right supportive framework in place, more parts be printed in the future as general practice.
Investing in 3D printing could be used to speed up repairs in workshops, and cut down on the distance that parts are shipped across the globe addressing well founded environmental concerns. We’re all know how far other parts of the industry are going to lessen the sector’s impact.
Ford is looking at the technology, as is Bentley, and Cupra is using 3D printing in its Extreme E race vehicles to name some of the biggest names interested. And given the emergence of metal printing technology, it may only be a matter of time before it using it to solve problems becomes more common practice.