How to put a stop to brake bearing problems: Part II
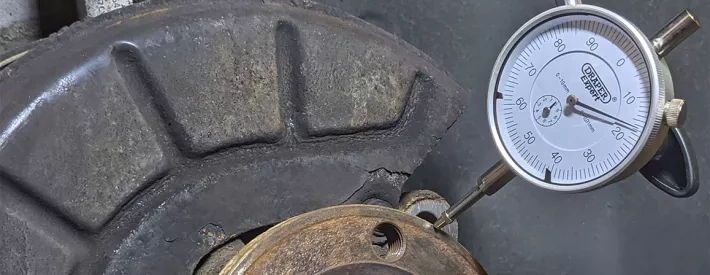
When wheel bearings fail – or they’re a concern – follow these seven tips to make sure you’ve done everything possible to keep your customer happy.
1. Underside inspection
Checking the rest of the vehicle underside is good practice, even if the vehicle is presented for wheel bearing concerns.
2. Evidence
Collecting evidence in case repairs are needed reassures motorists that everything you do is necessary. It also forms a record to protect the workshop if the motorist chooses to ignore your recommendations. Smart devices work well documenting this evidence incorporating different types of media. However, should you not have access to the technology, a well thought out inspection form is still better than no evidence at all. Remember to comply with GDPR.
3. Communication
The smart device has the expedient nature of built-in communication capability. Communications such as seeking authorisation for work are handy to encourage returning authorisation in the same format, giving a recording of authority to continue.
4. Post work road test
Following replacement, a post-work road test to check all symptoms have been resolved should be conducted. Although wheel nuts would have been torqued before exiting the workshop, a second check by a different technician is best practice. Ensure you record who made this check in the data capture process.
5. Invoicing
Detailing each measurement and repair in the invoice assists with the justification of cost. Paper-based forms can be used with carbon copy sheets, particularly if you have a clean and tidy workshop, or this information can be digitised. If a motorist returns following a wheel bearing replacement with a concern of premature brake failure, having the supporting data that shows you warned the motorist of this possibility puts to bed very quickly any complaints starting with “ever since you worked on my car...”
A digital invoice with an easy payment method can speed up the vehicle collection process and later bookkeeping.
6. Hand over
If payment has already been received, this is a good opportunity to discuss aftercare, prevention of premature component failure and/or showing your customer the removed components. Collecting payment at this point can sometimes eat into the available time for staff and motorists to complete this step.
7. Follow up
Premature failure is rarely a happy experience. Following up using your preferred communication method – telephone, text, email – can help with client retention and positive review acquisition. An offer for a free wheel nut inspection after 30 miles/50 km can be made at this point, and it’s advisable to include this ‘reminder to check’ in your invoice.