Understanding the importance of oil
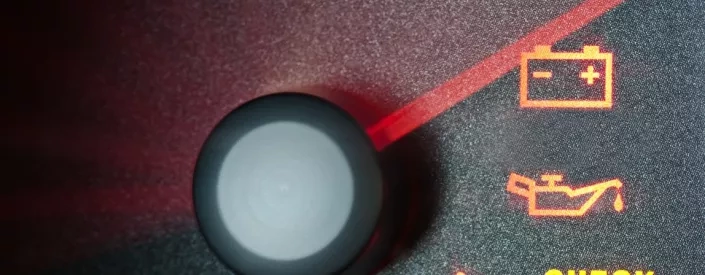
Modern engine design has placed greater demands on lubrication systems than ever before. Two areas where the importance of oil quality is most evident are in wet timing belt applications and diesel particulate filter (DPF) performance. Both systems rely heavily on the condition and specification of the engine oil, and misunderstanding this relationship can lead to costly failures.
Perfect timing
Wet timing belts, also known as belt-in-oil systems, have become increasingly common as manufacturers seek ways to reduce engine size and emissions without sacrificing performance. By running the timing belt inside the engine, lubricated by oil, friction is lowered, operating noise is reduced, and fuel economy can be improved. However, this arrangement introduces a new sensitivity to oil condition.
The materials used for wet belts are designed to operate within specific chemical limits. If the oil degrades – through oxidation, contamination, or extended service intervals it can lead to belt swelling, hardening, or cracking. These effects can cause timing issues, belt slippage, or in extreme cases, complete belt failure. Unlike dry belt setups, where physical wear is the primary concern, wet belts depend on stable oil chemistry for their survival. Manufacturers specify particular oil grades, often with stricter additive packages and lower ash contents, to ensure compatibility. Missing a scheduled oil change, or using a non-approved lubricant, significantly raises the risk of serious engine damage. This can then effect other parts of the engine, as the belt breaks down the small parts then enter the oil system, it can then clog the oil pick-up and filters causing low or no oil pressure which can then have serious effects on other systems such as the bearings or turbos. So missing an oil change or using the incorrect grade can run up a bill of thousands in repairs.
Filtering know-how
Parallel to this, diesel engines equipped with DPFs also suffer if oil quality is compromised. During normal operation, DPFs capture soot particles from the exhaust gases to reduce particulate emissions. To maintain functionality, these filters must periodically regenerate, burning off the trapped soot at high temperatures. Problems arise when vehicles used for short trips or urban driving cycles fail to reach the necessary conditions for passive regeneration.
When passive regeneration can’t happen, the engine management system initiates active regeneration, injecting additional fuel into the combustion chamber to raise exhaust temperatures. Some of this excess fuel can bypass the combustion process and dilute the engine oil. Over time, this oil dilution reduces the oil’s viscosity, diminishes its protective qualities, and introduces unburnt hydrocarbons back into the emissions system, including the DPF.
A heavily diluted oil not only risks engine wear but can contribute to ash formation within the DPF, shortening its service life.
Staying protected
Manufacturers attempt to mitigate these problems through the use of low-sulphated ash, phosphorus, and sulphur oils, which are designed to protect both the engine and the aftertreatment systems. Nevertheless, proper oil management is essential. Regular monitoring of oil condition, adherence to correct service schedules, and the use of manufacturer-approved lubricants are necessary to maintain both belt and DPF performance.
The move towards electrification and hybridisation isn’t lessening the importance of engine oil; in fact, it has made it more critical. Hybrid vehicles, with frequent engine stop-start cycles, place even greater demands on lubrication systems, while wet belt and emissions control technologies are continuing to evolve.
Understanding the relationship between oil quality and modern engine components is no longer optional for technicians. Whether dealing with a seemingly simple belt-in-oil design or a complex DPF-equipped diesel, the principle remains the same: the right oil, changed at the right time, is one of the most important defences against mechanical failure.