Putting the brakes on bad pad linings
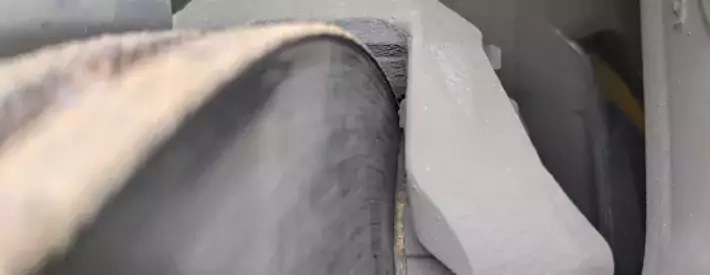
Numerous lockdowns have had an impact on cars, specifically the brakes, so make sure you know what to look out for
One in three presentations for MOT testing initially earn a reason for rejection. In the month of June 2021, nationally, 24.4% of those failures were due to brakes, the third most common reason for failure.
From a social media straw poll, motorist reported issues with brakes are on the increase, with noises and judder quite often prompting a visit outside of scheduled maintenance or MOT testing. Quite often these reported faults, although irritating, would meet the standard required for MOT testing – communication with the motorist of what is happening with their braking system is key in meeting expectations.
Replacing brake pads that appear to have plenty of friction material to a casual glance can be a difficult conversation with the vehicle presenter, understanding causation for prevention of future premature failure can soothe an abrasive conversation.
Over the lockdown period, long periods of idle time, coupled with the handbrake firmly on and perhaps more enthusiastic boredom washing than usual has contributed to poor brake component health. Overzealous use of cleaning products for a stood vehicle can accelerate corrosion related damage, resulting in premature wear. This problem is further exasperated by continuing inactivity, allowing the components to corrode into position.
April showers didn’t make for much of an appearance this year, but May made a credible effort to make up for that absence. By the middle of that month some areas in Britain had already received a month’s worth of corrosion inducing moisture from the skies.
Under-used vehicles can suffer issues with brakes due to corrosion and the pad material delaminates from the backing plate. A reason for rejection (RFR) in this situation is that the brake lining or pad is not missing, but it is now incorrectly mounted.
Delamination can also be caused by thermal destruction, mechanical influence (a wobbly wheel bearing, a dropped component prior to fitting perhaps?) and in rare cases, faulty production.
Underlying corrosion can be an increasing presentation and cause the material to completely part company with the backing plate. Thermal stress can present a hardened material with discolouration, mechanical influence may present a new looking pad with stress points, and a production issue should not show signs of corrosion, but rather a new looking component with insufficient bonding between the pad and the plate.
Thermal stress has also contributed to brake pad delamination, government statistics showing the relationship between the quieter roads of the lockdown and speeding offences have placed many components under stress. Hard use followed by inactivity, an over enthusiastic cleansing of brake dust from wheels, followed by a particularly wet weather month has created a perfect set of conditions for premature failure. It should be noted that all aspects of this recipe for disaster aren’t always necessary for delamination, but education about causation can help reduce the number of replacements required.
Inspecting brake components should always be a careful and thorough method of inspection (MoI), but as corrosion related cases increase, signs to lookout for, including the obvious corrosion of a brake disc include:
- Noise from the brakes when entering the testing facility
- Feedback from the motorist of the brakes not feeling or sounding “right”
- Inspection of the pad material shows the friction material breaking away or severe cracking* (if you are lucky enough to get a good view)
- Rotation of the wheel shows the pad shifting in the caliper whilst the ears of the backing plate are firmly held
- Signs of thermal damage from other components (such as the disc) as thermal damage can be difficult to see with the prescribed MoI
Accredited training can be a huge source of reassurance for those members of the team relaying bad news to the motorist, in addition to the continuous professional development afforded to technical staff. Effective understanding and communication will be required for all motorists, but empathy may be needed in the case of premature failure in more difficult financial circumstances.